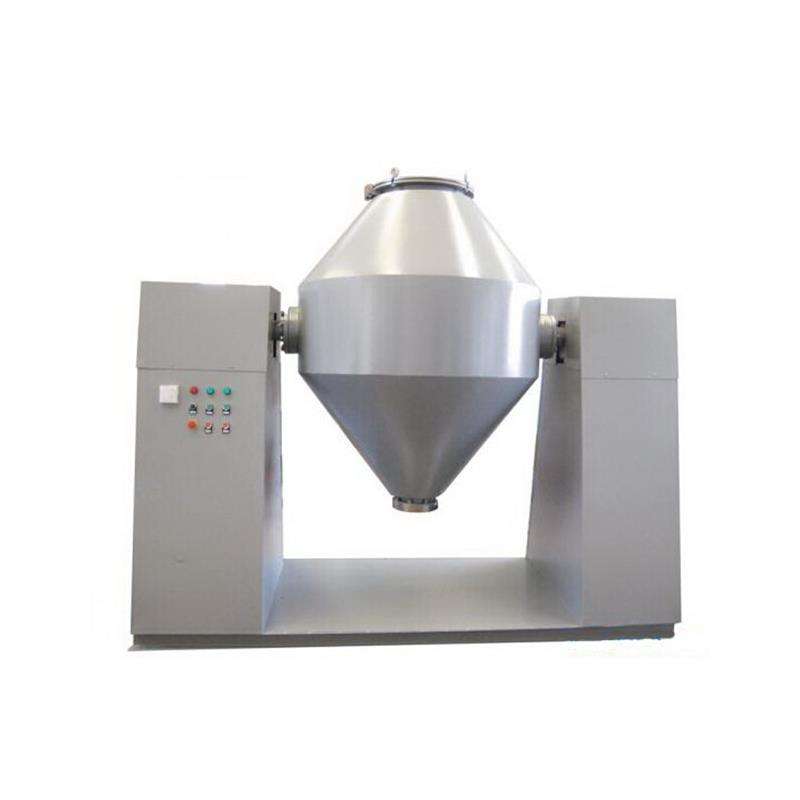
1、双锥回转真空干燥机的经典性
双锥回转真空干燥机是原料药生产应用较为广泛的设备,这是由于在真空干燥的过程中,筒体内的压力始终低于大气压力,气体分子数少,密度低,含氧量低,因而能干燥容易氧化性变化的药品生产,能减少物料染菌的机会。也由于水在汽化过程中,其温度与蒸汽压力成正比,故真空干燥时物料中的水分在低温下就能汽化,达到低温干燥,特别适用于药品中有热敏性物料的生产。同时,真空干燥可消除常压热风干燥易产生表面硬化现象,这是真空干燥物料内和表面之间压差大,在压力梯度作用下,水分很快移向表面,不会出现表面硬化。此外真空干燥时,物料内部和外部之间温度梯度小,由逆渗透作用使得溶媒能够独自移动并收集,有效克服热风干燥所产生的溶媒失散现象。
从功能上看,双锥回转真空干燥机是集混合、真空干燥于一体的干燥设备,它以简洁、方便和双效特点被人们作为经典设备来应用,其有着实用性和经济性的一面,是其它设备难以替代的。
2、对双锥回转真空干燥机提高思路的探讨
虽然,双锥回转真空干燥机被人们看作经典,但近几年来却又被药厂所淡化了,其根本原因是由于制造商缺乏对其的研究和结构的改进所致,其主要表现在结构上难以CIP/SIP和干燥性能优化上,故有必要对其提高思路作一探讨。
2.1、对双锥回转真空干燥机的干燥速度的探讨
2.1.1、真空干燥速度的概念
文献认为:物料的干燥过程,首先是物料表面的水分受热汽化并被真空设备排除,物料表面的水分因汽化而逐渐减少,并在物料内部与表面之间形成温度差。内部的水分在温度差的作用下,不断向表面扩散,并在到达表面后汽化。另外,在真空干燥过程中,同时存在着压力差,使得被汽化的水分子加速向真空空间移动。在真空干燥过程中,人们总是希望加快干燥速度,缩短干燥时间,但是影响干燥速度因素1有以下几点:
(1)被干燥物料的状况(如物料形状、大小尺寸、堆置方法),物料本身的含湿量、密度、粘度等性能。一般,物料颗粒细而均匀、堆放松散、厚度薄,则内部水分容易扩散。若提高物料的初温、经真空过滤前处理、降低物料含湿量等,均能提高真空干燥速度。
(2)真空度越高,越利于水分在较低温度下汽化,但真空度过高不利热传导,会影响对物料的加热效果。为提高物料干燥速度,应根据物料的特性综合考虑真空度。通常,真空度应不低于1×104Pa。
2.1.2、影响双锥回转真空干燥机干燥速度的因素
文献把双锥回转真空干燥机干燥过程作试验,分别以真空度、干燥温度、蒸汽压力与干燥时间为参数,试验所作的曲线表明:双锥回转真空干燥机干燥过程可分为第一升温、第一恒温、第二升温、第二恒温和降温五个阶级。其中:(1)第一升温是加热物料,使其升温的预热阶段。该阶段中,物料中水分汽化量很少;(2)第一恒温是恒速干燥阶段,在该阶段中,物料的自由水、表面水和毛细管水等大量汽化。因此,温度和真空呈恒定状态,且真空度与该干燥温度下水的饱和蒸汽压力近似相等;(3)第二升温是加热物料迁移内部水分至物料表面的过程,由于汽化的水分很少,导致物料温度升高和真正度也随之提高;(4)第二恒温是汽化物料包裹水和部分结晶水阶段,由干水分迁移率与汽化率相定,故温度和真空呈平稳状态;(5)降温阶段开始时,关闭加热蒸汽,通以冷却水至筒体夹套,冷却筒体使其内部物料温度下降,以便卸出干燥制品。
2.1.3、双锥回转真空干燥机旋转速度对真空干燥速度的影响及探讨
双锥回转真空干燥机筒体的旋转速度越快,干燥速度越高。但在干燥后期,随着物料湿含量的下降,干燥速度也降低,此时提高转速对干燥速度的提高均无益。另外,在干燥初期,较快的旋转速度,会导致湿分汽化过快而产生物料粘结成团的现象。因此,应在干燥初期采用较低的转速,待物料表面较干以及不结团时再提高转速,以便加快干燥速度、缩短干燥时间。
对此点,建议可选用变频电机,使筒体的旋转速度在运行时能变动,并有菜单可设定不同时间段所选用的不同的筒体旋转速度(0~10rpm内无级调速),即要有时间—速度关系的设定。
2.1.4、双锥回转真空干燥机加热与冷却对真空干燥速度的影响及探讨
双锥回转真空干燥机夹套内对流换热需分别提供热量和冷量,故夹套内将经历以热蒸汽方法的升温或以冷却水方法的降温。文献1认为,提高热介质温度可加快升温速度,缩短干燥时间。对粘性大的物料,热介质温度高容易产生结团现象。降低冷却水温度可加快降温速度,也可缩短工作周期。随着物料的性质不同,可选择适当的温度,常以变温干燥法为佳,即在干燥初期温度低,逐渐提高温度以增大干燥速度。
对此点,建议可选用温度传感元件,使双锥回转真空干燥机夹套内热量或冷量控制能在运行时变动,并有菜单可设定不同时间段所选用的温度,即要有时间—温度关系的设定。
2.1.5、双锥回转干燥机真空度对真空干燥速度的影响及探讨
通常双锥回转真空干燥机选用1×103-1×104Pa真空度,真空度高,物料中湿分汽化温度低,干燥速度快。但真空度过高,会导致抽气系统成本增加,干燥后物料价格增高,经济上不合算。但表1可知,在降温阶段的真空度值很小,故应分段来控制真空度的压力。
对此点,建议可选用压力传感元件,使双锥回转真空干燥机筒体内真空度控制能在运行时变动,并有菜单可设定不同时间段所选用的真空度,即要有时间—真空度关系的设定。
2.1.6、双锥回转真空干燥机锥体角度及充填量对真空干燥速度的影响
双锥回转真空干燥机筒体堆放颗粒状或粉末状物料时,当物料堆斜面与底面间夹角增大到某个角度时,将发生侧面物料下滑落的现象。此时发生物料滑落的斜面与底部的夹角称该物料的滑移角(滑移角与物料组成、湿含量、粒度和粘度有关)。故双锥回转真空干燥机的设计和选择时,应根据物料的滑移角而选择锥体的角度1。
文献1也认为,实际装料容积与干燥筒体容积之比为充填率。双锥回转真空干燥机的充填率通常为30%~50%之间,其与物料的堆密度也有关。
从上可知,双锥回转真空干燥机筒体锥体的角度太大或太小都会影响翻动混合效果,而其形成的物料干燥表面最终影响了干燥速度。同样,实际装料容积充填率过高也会影响翻动混合效果,影响了干燥速度。
2.2、对双锥回转真空干燥机的结构的探讨
虽然双锥回转真空干燥机有着许多实用性优点,但结构上的不完善阻碍了其应用和发展。特别对应用于无菌原料药生产来说,尚未改进设备所存的不完善之处表现为:(1)抽真空管空套回转轴的动静密封件泄漏与清洗问题;(2)筒体结构的清洗或灭菌问题;(3)进料/出料结构的易出料与清洗问题。
2.2.1、抽真空管空套回转轴的动静密封件泄漏与清洗的探讨
在部分双锥回转真空干燥机的抽真空管空套回转轴装置中,其采用双骨架轴密封结构,由于此结构密封的不可靠,在筒体抽真空的作用下极易造成泄漏,有时会出现所谓的“漏油”现象。同时,也由于密封的不可靠会在干燥时结存粉,此处的结存粉用普通的旋转动态水洗方法是难以洗净的,这样会引起换批时的交叉污染。
近期国内有制造商对此作了一定的改进,有的采用特殊密封(如特殊的机械密封、磁流体密封等)。也有的制造商2在抽真结构上作了改进,使抽真空部分不伸进筒体内部,仅在旋转筒体外面与其接触,采用金属烧结网做过滤器,容易清洗,容易消毒灭菌,并配有用高纯氮气反吹的系统,防止粉尘物料堵塞过滤网孔,确保真空畅通。
2.2.2、筒体结构的清洗和灭菌问题的探讨
在部分双锥回转真空干燥机筒体的清洗中,有的靠切换真空管路,放入清洗水旋转筒体再放净,这样动态清洗法是无法彻底洗净的,至少在动静接触面和结料处是不能洗净。
其次是部分制造商没有把筒体当作压力容器来设计及制造,很难做到切换真空管路通入蒸汽来灭菌,故谈不上蒸汽的在位灭菌。这里当然涉及到进料/出料结构与密封结构,其形式和承压性能也与蒸汽灭菌有关。而在无菌环境使用设备的至关重要要求就是清洗后的灭菌,通常灭菌的方法中最有效和直接的方法是湿热和干热灭菌,基于该设备筒体结构是不可拆的,不能采用干热灭菌,只能采用湿热(蒸汽)灭菌。
对此,说白了就是设法方便清洗和灭菌,也只要能围绕此专题所展开即可。近期国内有制造商对作了一定的改进,在清洗方面,采用靠切换真空管路,放入加压的清洗水旋转筒体,再放净的方法,虽然有所提高,但实效也不是十分理想。在灭菌方面,有的制造商在制造筒体和料阀方面考虑到承压性,其可采用切换真空管路而通入蒸汽也完成SIP。
2.2.3、进料/出料结构的易出料与清洗性的探讨
此问题虽说是上述问题的延伸,但进料/出料的特殊要求是易放净、易操作、易清洗/灭毒。国内部分制造商采用蝶阀或可拆卸结构,也取得了一定成效,但对照GMP和相应工艺要求,这里可展开的研发是大有文章可做。
2.3、双锥回转真空干燥机提高的一点思路
至于双锥回转真空干燥机要提高的话,可以研发的思路很多,笔者感到还可尝试以下几个思路,这里仅为思考性及建议性的设想。
2.3.1、拓广双锥回转真空干燥机的功能,以适应更大的应用
(1)增加搅拌和造粒功能。可在双锥回转真空干燥机的抽真空管中穿入一个带喷嘴的管(能喷粘合剂),同时真空管进入筒体内部处增设一个固定搅拌叶片。当筒体转动过程中,固定在抽真空管上搅拌叶片迫使物料从其两侧面流过,这样在物料沿筒壁滑动的同时,又增加了径向运动。因此,能有效地提高了混合和搅拌物料的效果,加快了湿分汽化,提高了干燥速度。尔后在粉体物料工艺结束时,可由穿入带喷嘴(能喷粘合剂的管)喷出相应粘合剂,将粉末状干物料制成颗粒状制品。
(2)增加搅拌和粉碎功能。国内有的制造商采用破碎装置2,该装置的刀具为四把组合整体结构,采用十字交叉排列,由短到长,依次焊接,刀具采用不同的长度,不同的角度。确保旋转时能与物料充分接触,保证破碎效果。这样物料在双锥回转筒体内不停地翻动,并与筒壁进行热交换(筒壁外面半剖盘管用热水进行循环加热)。在双锥筒体旋转时破碎刀同时转动,每当筒体旋转一圈,物料与破碎刀接触一次。由于破碎刀的转速较快(最高为250rpm),而筒体的转速较慢(一般为3rpm),故每当物料与刀具接触时,破碎效果十分明显,筒体内系统在真空下运行。
2.3.2、构筑双锥回转真空干燥机系统设计的概念,以适应生产率的提高
双锥回转真空干燥机能在生产中有效应用的话,必然是一个系统的概念,其中有机溶剂收回系统是一个关键的过程。制造商在供应双锥回转真空干燥机设备时,不能只提供单机,而是应提供系统,应考虑有机溶剂的回收,由于溶剂的沸点较低,故采用冷冻水进行冷凝冷却,确保溶剂能回收利用,避免被真空泵抽走后污染大气。
2.3.3、研发CIP/SIP结构,以适应无菌级的生产
关于双锥回转真空干燥机的CIP/SIP结构应该换个思路去研发其结构,除上所谈及的思路外,还能通过快开式外接喷淋清洗装置,当停机时接入筒体,并形成清洗环路系统。也可设想整个双锥回转真空干燥机的筒体能拆卸(如夹持式方锥形混合机结构),这样整个筒体能进入清洗站内完成清洗及灭菌,当然此设想的难度太大。而此点也是双锥回转真空干燥机能升级换代的基础,使其能适应无菌级的生产。
3、双锥回转干燥机优化组合产品---多功能干燥设备的介绍
3.1、多功能干燥设备的组成和特点
3.1.1、多功能干燥设备的组成
多功能干燥设备基本示意如图1与图2(设备旋转180°后示意)所示,其由抽真空接口1、进料快开接口2、防爆箱3、喷淋装置4、烧结网抽真空滤棒5、内胆、夹套和保温材料6、单抽滤用快开阀7、抽滤用烧结网8、热水进口9、热水出口10、防爆控制面板11、防爆电机12、减速机13、压力表14、搅拌叶15、罐体16、主轴17和底座支架18等组成。
3.1.2、多功能干燥设备的特点
多功能干燥设备利用罐体旋转、不同位置的静止,再配以搅拌叶、烧结网抽真空滤棒和抽滤用烧结网等装置,进行不同的组合来达到完成传统反应、结晶、浓缩、抽滤、洗涤与干燥设备基本功能,其不同组合则通过PLC控制来完成。新颖多功能干燥设备与其它结晶类原料药生产设备相比有以下几个主要特点:
(1)在反应、结晶、浓缩整个工艺过程中,物料在多功能干燥设备内经反应、结晶、浓缩工序后,无需通过管道输入下道工序,避免了由于管道繁琐而造成的药物浪费、交叉污染以及多次清洗消毒(灭菌)问题,能防止了有可能出现的泄漏、混批、污染或其它危险事故的发生。
(2)在抽滤、洗涤工艺过程中,多功能干燥设备能克服原工艺配置的抽滤器、离心机、压滤机等设备所造成的效率低、“毛点”超标、操作强度大、资源浪费、难以清洗消毒(灭菌)以及占地面积大等缺点。
(3)在干燥工艺过程中,多功能干燥设备能克服原工艺配置的干燥箱或双锥回转干燥器等设备所存在的劳动强度大、干燥过程中容易“结块”或“起球”、干燥速度慢和有可能出现“混批”现象等问题。
(4)该设备所有附件均可单独拆洗与消毒(灭菌)。
3.2、多功能干燥设备的应用方案
3.2.1、应用方案1
如图1,首先多功能干燥设备在罐体静止状态下,物料通过进料管2由喷淋装置4进入罐内进行进料、反应、结晶、浓缩等工序生产,整个罐体16底部设计为圆锥形,罐内无明显死角。在密闭状态下,通过搅拌叶15的旋转对物料不断翻动,能使物料在反应、结晶、浓缩的过程中更均匀。搅拌叶15的形式可以根据物料与工艺要求配置不同的叶片,搅拌转速则通过变频器设置,也可用调速减速机13手动调速。同时,搅拌器由防爆电机经过减速机驱动,电源由主轴17一端通过防爆箱3顺着旋转罐体圆锥面引入。其中,设备的控制面板11亦采用防爆设计,并通过机械密封达到优越的密封性能,保证操作在严格无菌条件下进行。
在反应过程中,可摆动(+/-30?)锥体形罐体,以达到搅拌更均匀的效果。同时,在进行这几道工序时,罐体16可以加热或冷凝,根据不同物料和工艺要求在夹套6内通入不同的热交换介质来控制所需温度。
进行结晶与浓缩后(如图2),罐体16位置转动180°则可进入抽滤阶段。此时,关闭搅拌器15,接上抽真空接口1,抽真空接口1上带有快开接口2,从快开接口2通入氮气,对滤饼压滤或进行抽真空抽滤,使固液在密封的情况下进行分离,其抽滤所用的烧结网8可采用烧结网或四氟烧结过滤板、滤布等,并可以拆卸。
抽滤结束后,通入进料管2由喷淋装置4通入洗涤液,转动罐体16,启动搅拌器15,让物料进一步纯化。也可不转动罐体16,只通过喷淋装置4喷入洗涤液,对物料进行浸泡、洗涤、纯化。纯化到指定要求后,将有烧结网8的一端朝下,进行再一次压滤式过滤。
洗涤、抽滤结束后,在抽滤快开接口7通入正压空气或氮气,反吹滤饼,使滤饼和过滤板脱离,再转动锥体形罐体,启动破碎装置。此时,罐体转动也带动滤饼转动,滤饼转动过程中接触到破碎装置即可粉碎,以防止在回转干燥过程中滤饼成团结块。同时,在夹套6内通入热源,并在抽真空口1进行抽真空干燥,直达到干燥要求的指标。其中,为防止真空管与轴之间摩擦所产生的金属屑进入物料内,真空管的抽真空头做成烧结网抽真空滤棒5。为增加抽真空面积,真空头设计成四个,而且跟罐体16一起旋转,并可单独拆下更换和清洗。
3.2.2、应用方案2
如图1,多功能干燥设备设备首先在静止状态下进行进料、反应、结晶、浓缩等工序。先将设备罐体转至搅拌叶15一端锥体位置朝下,此时设备类似于一个带有侧搅拌的反应罐。盖上两端盖,在快开接口2内通入需要反应的不同物料。进料结束后,由于物料在反应过程中需要控制不同的温度,则通过对夹套6通入不同的热源来控制反应所需的温度。如在反应过程中物料的温度不可超过80℃,则通入冷却水来控制反应温度。当反应结束后,在结晶过程需要30℃的温度,那可以在夹套内通入30℃的水,使结晶过程的温度始终保持30℃。等浓缩过程结束后要进入下一步过滤阶段。
进入抽滤阶段前,将设备锥体形罐体位置旋转180°,使装有抽滤用烧结网8的一端锥体朝下,接上抽真空接口1,打开放液球阀,让母液和结晶体分离。在分离过程中,由于设备是在密闭情况下操作的,在原来的快开接口2上可以通入氮气或压缩空气,并可以抽真空,以提高过滤速度,使母液可以更快、更彻底地与结晶体分离。
抽滤结束后,在快开接口2上切换进入清洗液,通过喷淋装置4让洗涤液均匀地分布在物料的上部,并进行浸泡,或转动锥体,同时启动搅拌叶15,使物料和洗涤液充分洗涤,让残留在物料表面的母液得到更充分地洗涤。
洗涤结束后,重复抽滤过程,使固液分离,达到10%--15%的含水量要求时,可以让物料进行干燥。此时,关闭放液阀,拆除排液管,对夹套6通入干燥热源,一般物料的干燥温度控制在100℃以下,由进入夹套6的热源来控制干燥所需温度,同时通过真空泵抽真空来带走蒸发出来的水蒸气,也可以在真空泵前加装一个冷凝器来回收溶媒。另外,在端盖一端设置一个原位取样口,可以检测干燥物料在不同时间段内的物料干燥程度。此外,根据物料的特性,还可以在干燥过程中通过进料管2由喷淋装置4通入氮气,既加快干燥速度,有能保护物料在干燥过程中不至于破坏特性。在这样的工作条件下,一般只需3—4个小时就能把物料烘干。
由于物料在回转干燥过程是在作圆周运动,一些带有粘性的物料特别容易“起球”,起球后在球的内部不易干燥,还易结块,这样就很难控制物料的水分和色泽。在此种情况下可以启动搅拌装置,当设备转动一周,粉体就和搅拌叶15接触一次。一般在转动过程中,搅拌叶15与物料接触的时间为1/3转。搅拌叶的转速通过变频器调节最高可达到280转/分。这样,物料在回转干燥过程中的起球、结块问题就能解决了。
想要了解更多干燥设备信息,请关注常州市范群干燥设备有限公司 www.fanqun.com